DIY Guide to Building Conveyor Rollers
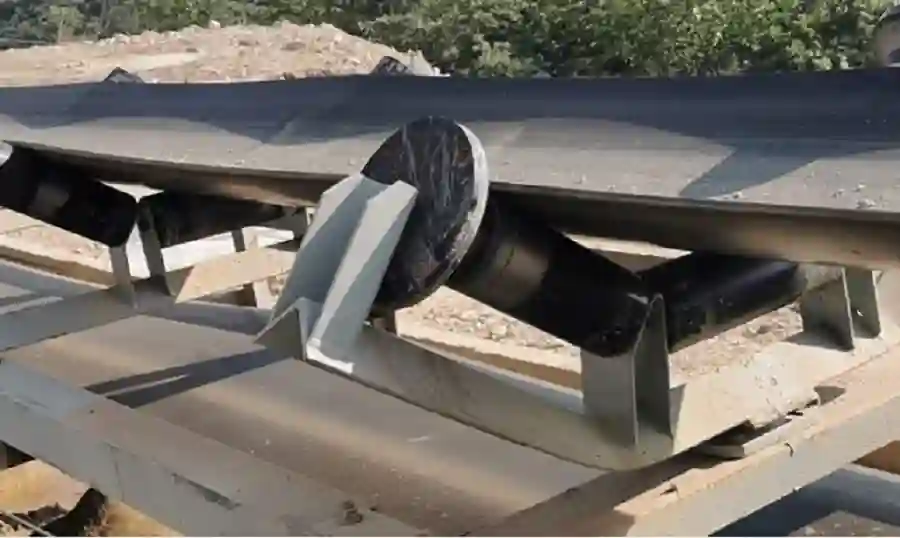
Conveyor rollers are crucial components in custom conveyor systems, facilitating the smooth and efficient movement of materials. They play a vital role in enhancing productivity and streamlining operations across various industries, including manufacturing, logistics, and warehousing. By ensuring reliable and consistent transportation of goods, conveyor rollers help reduce manual labor and improve overall system efficiency.Building your own conveyor rollers can be a cost-effective and customizable solution for specific applications. DIY conveyor rollers allow you to tailor the design and materials to meet unique requirements, whether for hobby projects, small-scale production, or specialized industrial tasks. This approach not only saves money but also provides the flexibility to innovate and optimize your material handling processes according to your specific needs.
Types of Conveyor Rollers for DIY Projects
PVC Conveyor Rollers
PVC (Polyvinyl Chloride) conveyor rollers are a popular choice for DIY projects due to their versatility, cost-effectiveness, and ease of use. Here are some benefits of using PVC in DIY conveyor roller projects:
Lightweight and Durable: PVC is lightweight, making it easy to handle and install. Despite its lightness, it is also durable and can withstand various environmental conditions, including exposure to chemicals and moisture.
Cost-Effective: PVC pipes are relatively inexpensive compared to other materials, making them an economical choice for DIY projects. They are readily available in various sizes, allowing for customization without significant expense.
Easy to Work With: PVC can be easily cut, shaped, and assembled using standard tools, which simplifies the DIY process. Its smooth surface reduces friction, ensuring efficient material movement along the conveyor system.
Customizable: PVC rollers can be customized to fit specific project needs, whether for light-duty or medium-duty applications. They are ideal for creating prototypes, small-scale production lines, or hobbyist projects where flexibility and adaptability are key.
Conveyor Roller Balls
Conveyor roller balls, also known as ball transfer units, are specialized components that enable multi-directional movement. Incorporating ball transfer units in DIY builds offers several advantages:
Multi-Directional Movement: Unlike traditional rollers that facilitate linear motion, ball transfer units allow materials to move in any direction with ease. This is particularly useful in applications requiring precise positioning, sorting, or rotating of items.
Smooth Operation: Ball transfer units provide a smooth and low-friction surface, reducing the effort needed to move heavy or awkwardly shaped objects. This can enhance the efficiency of material handling processes.
Versatility: These units can be integrated into various DIY conveyor systems, including transfer tables, turntables, and sorting stations. They are suitable for handling a wide range of items, from small packages to large, heavy loads.
Durability: Made from robust materials like steel or stainless steel, ball transfer units are designed to withstand significant wear and tear, ensuring longevity and reliability in DIY applications.
Nylon Conveyor Rollers
Nylon conveyor rollers are another excellent option for DIY projects, offering specific benefits that make them suitable for various applications:
High Strength and Low Weight: Nylon rollers combine high strength with low weight, making them easy to handle and install while providing excellent load-bearing capabilities. This balance is ideal for DIY projects that require durable yet manageable components.
Chemical and Abrasion Resistance: Nylon is resistant to chemicals and abrasion, making these rollers suitable for environments where they may be exposed to harsh substances or require frequent cleaning.
Smooth and Quiet Operation: Nylon rollers operate smoothly and quietly, reducing noise levels in the working environment. This is particularly beneficial in settings where noise reduction is important.
Readily Available: Nylon rollers are widely available and come in various sizes and configurations, making them a convenient choice for DIY enthusiasts. They can be easily sourced from local suppliers or online retailers.
By understanding the different types of conveyor rollers available for DIY projects—PVC, conveyor roller balls, and nylon—DIY enthusiasts can select the most appropriate materials for their specific needs. This ensures that their custom conveyor systems are efficient, cost-effective, and tailored to their unique requirements.
Materials and Tools Required
Essential Materials
When embarking on a DIY conveyor roller project, having the right materials is crucial for building a functional and durable conveyor system. Here are some essential materials you will need:
PVC Pipes: These are the primary components for making PVC conveyor rollers. Ensure you choose the appropriate diameter and wall thickness to handle the load and fit within your conveyor system’s specifications. PVC pipes are lightweight, durable, and easy to work with, making them ideal for DIY projects.
Nylon Rollers: For projects that require pre-made rollers, nylon rollers are a great option. They offer high strength, low friction, and excellent resistance to chemicals and abrasion. Nylon rollers are versatile and can be used in various conveyor applications.
Ball Units: Also known as ball transfer units, these components are essential for creating multi-directional movement in your conveyor system. They consist of a large load-bearing ball housed within a casing that contains smaller support balls, allowing for smooth and versatile movement of materials.
Brackets: Brackets are used to mount and support the rollers within the conveyor frame. They help ensure the rollers are securely held in place and properly aligned. Brackets come in various sizes and materials, including steel and aluminum, to suit different project needs.
Bearings: Bearings are crucial for allowing the rollers to rotate smoothly. Depending on your roller design, you may need bearings that fit inside the PVC pipes or those that support the ends of nylon rollers. Choose high-quality bearings to ensure longevity and reliable operation.
End Caps: These are used to secure bearings within PVC pipes, preventing them from moving and ensuring the roller rotates correctly. End caps also help protect the bearings from dust and debris.
Tools Needed
Having the right tools is essential for cutting, assembling, and installing conveyor rollers. Here’s a list of necessary tools for your DIY project:
Measuring Tape: Accurate measurements are crucial for ensuring all components fit together correctly. Use a measuring tape to measure the lengths of PVC pipes and the spacing between rollers.
Marker: A marker is useful for marking cutting lines on PVC pipes and other materials, ensuring precise cuts.
Saw: A hand saw or a power saw (such as a miter saw) is needed for cutting PVC pipes and other materials to the desired lengths. Ensure the saw blade is suitable for cutting plastic to achieve clean and smooth edges.
Drill: A drill is required for creating holes in PVC pipes, brackets, and other components for mounting and assembly. Use drill bits of appropriate sizes to match screws and bolts.
Screwdriver: A screwdriver is essential for assembling components, such as attaching brackets and securing end caps. Depending on the type of screws used, you may need a Phillips head or flathead screwdriver.
Wrench: A wrench is useful for tightening nuts and bolts during assembly. An adjustable wrench or a set of wrenches in various sizes can help accommodate different fasteners.
File or Sandpaper: After cutting PVC pipes or other materials, use a file or sandpaper to smooth out rough edges and burrs, ensuring safe handling and assembly.
Level: A level helps ensure that your rollers and conveyor frame are properly aligned and level, which is crucial for smooth operation.
Safety Gear: Safety should always be a priority when working on DIY projects. Wear safety goggles to protect your eyes from debris, gloves to protect your hands, and a dust mask if cutting materials that produce dust.
By gathering these essential materials and tools, you can confidently tackle your DIY conveyor roller project, creating a custom system that meets your specific needs and enhances your material handling capabilities.
Step-by-Step Guide to Building PVC Conveyor Rollers
Planning
Before starting the construction of your PVC conveyor rollers, careful planning is essential to ensure the system meets your specific needs and functions effectively. Here are the key steps in the planning phase:
Define the Purpose: Determine what you need the conveyor system for. Consider the types of materials it will transport, the load capacity, and the operational environment.
Sketch the Design: Create a detailed sketch of your conveyor system, including dimensions, roller spacing, and the overall layout. This will serve as a blueprint for your project.
Calculate Roller Requirements: Based on the length of the conveyor, calculate the number of rollers needed and their spacing. Ensure that the spacing is appropriate for the size and weight of the materials being transported.
Select Materials: Choose the appropriate PVC pipes, bearings, brackets, and other components based on your design specifications. Ensure that all materials are compatible and suitable for the intended application.
Cutting and Preparing Materials
Once the planning is complete, proceed with cutting and preparing the materials for your PVC conveyor rollers:
Measure and Mark: Use a measuring tape and marker to measure the PVC pipes according to the roller lengths specified in your design. Mark the cutting points clearly.
Cut the PVC Pipes: Use a saw (hand saw or power saw) to cut the PVC pipes at the marked points. Ensure the cuts are straight and smooth to facilitate proper assembly.
Smooth the Edges: After cutting, use a file or sandpaper to smooth out any rough edges or burrs on the PVC pipes. This will prevent damage to the bearings and ensure a snug fit.
Drill Holes for Bearings: If your design requires holes for securing bearings, use a drill to create appropriately sized holes in the PVC pipes. Ensure the holes are precisely located to maintain proper alignment.
Assembly
With the materials prepared, you can now assemble the PVC conveyor rollers:
Insert Bearings: Insert the bearings into the ends of the PVC pipes. If using end caps, secure the bearings inside the caps before attaching them to the pipes. Ensure the bearings fit snugly and can rotate freely.
Attach End Caps: Secure the end caps (with bearings) to both ends of the PVC pipes. Ensure they are tightly fitted to prevent movement during operation.
Mount Rollers on Brackets: Attach the assembled PVC rollers to the mounting brackets. Use screws or bolts to secure the brackets, ensuring the rollers are properly aligned and can rotate without obstruction.
Check Alignment and Rotation: Test the alignment and rotation of each roller. Ensure they spin smoothly and are parallel to each other. Adjust as necessary to achieve proper alignment.
Installation
The final step is to install your custom PVC rollers into the conveyor system:
Prepare the Conveyor Frame: Ensure the conveyor frame is clean and free of debris. Check that the frame is level and stable.
Install Rollers into Frame: Place the assembled PVC rollers into the conveyor frame, aligning them with the pre-drilled mounting holes. Secure the rollers using screws or bolts, making sure they are evenly spaced and aligned according to your design.
Test the System: Once all rollers are installed, test the conveyor system by running it without a load first. Check for smooth operation, proper alignment, and any unusual noises or vibrations.
Adjust as Needed: Make any necessary adjustments to the roller alignment or spacing to ensure optimal performance. Tighten any loose fasteners and recheck the system’s operation.
Load Test: Finally, test the conveyor system with the actual materials it will transport. Observe the rollers’ performance under load, and make any additional adjustments to ensure efficient and reliable operation.
By following this step-by-step guide, you can successfully build and install PVC conveyor rollers tailored to your specific needs. This DIY approach allows for customization and cost savings while providing an efficient solution for material handling.